Vision-based systems are getting more popular these days in the industry as they achieve good results and accuracy. They can replace multiple hardware sensors with a single camera, and such a system provides more accurate detection options and significantly reduces the cost of the technologies used.
We know 2 types of systems. The first type are Vision-based navigation systems based on geometrical calculation relating extracted features and template matching techniques.
The second type are Vision technologies based on neural networks. Their excellent results and performance inspired us here in M2Ms to look into them deeply. Neural networks represent flexible robustness in various lighting conditions, image degradation that can interfere with the image. We can effectively recognize objects in a few milliseconds with very high accuracy, even if they are rotated or seen from an angle.
We currently focus on the several use cases, where we are able to increase efficiency and quality of processess.
Object detection
In the field of logistics, we can use reliable image recognition using neural networks, which we use to recognize and count elements (components, goods, people). Individual training of a "neuron" takes about 1-2 days.
Precise and robust solution
Cheaper setup than conventional solutions
Possibility of OEE support - detection and counting of machine output, visual detection of machine status
Scalable inputs - possibility to recognize objects of different sizes (e.g. forklift 416x416, small objects 1280x1280)
Usage: object tracking (positioning), counting, presence of a specific object, inventory, recording the presence and identification of people, etc.
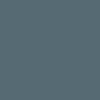
Vision in the warehouse
Based on a trained "neuron", we can reliably detect the positions of trucks, alert drivers and people in time to avoid collisions in the workplace. Our solution using camera systems is much more robust, simple and cheaper than conventional commercial solutions.
Solution:
Hazard avoidance - creating safety zones for forklifts and people by using lights and marking of specific areas of movement
Traffic management - avoiding occupancy in the loading/unloading positions, manage traffic at the crossroads to avoid collisions
Distance measurement and remote 360 - use of sensors on forklifts to sufficiently alert people/other truck drivers with horn, light, tablet to prevent collisions
OEE support - forklifts tracking and route optimization
The most common problems in the warehouse:
Forklift vs. forklift/people collision - lack of forklift driver’s visibility of obstacles due to oversize loads and insufficient traffic management
Occupancy of loading/unloading positions - emerging downtimes and traffic jams
Low safety level - risk of goods damage or employee injury
Vision face recognition & pose estimation
More accurate face detection with face recognition is a big advantage when using the Pick to Light (M2L) system, as operator and selection pairing is possible. In this way, a more accurate inspection can be performed. A more robust camera solution can be installed much faster and without the need for support using monitors and plug & play.
The most common problems in the company premises:
False entry - problems with missing cards, unattended entries
Occupancy of common areas - (dining room, changing room, toilets, etc.) emerging downtimes and long waiting lines, wasting working time of employees
Safety measures - the need for notifying people to avoid risk of getting injuries in time at the specific areas at the workplace
Solution:
Attendance system & person tracking - using the camera for detecting people for automatic attendance to the company premises and to avoid false entry
Face recognition with face masks on - possibility to identify the person wearing a facemask
Possibility to use Veasy (Visitor Management System)/own attendance system with extension - using the camera for entrance
Limited access - using camera and sensors for counting people and time spend in common areas, LED lights to show occupancy
Safety/forbidden zones observation - using camera and designate specific areas with lights to alert people in real time to avoid risk of getting injuries of employees
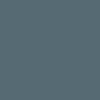
Vision object detection and human/hand recognition
There are 2 types of usage, with more precise pick detection, more robust and much cheaper solution. Simple installation with plug & play and easy setup can guarantee immediate use.
Conveyor application (yolo & mediapipe)
Goods tracking on conveyor
Detection of picking from conveyor
Live preview (on monitors –without LED)
Moving light (with LED conveyor)
Multiple picks
Combination with person recognition can track whole process without QR codes
Ikea style mount camera, configure system via live view and use
PTLs application (yolo & mediapipe)
Automatic layout setting
Auto alignment
Avoid double pick issue
More gestures
Multiple picks
Corrupted LED detection & hot fixing
Ikea style mount camera & strips and user configure system via live view
Vision autonomous navigation
Autonomous camera navigation for mobile robots and drones can provide:
Autonomous space mapping based on camera images
Route planning
Avoiding hazard and obstacles on the route in real time
Usage:
Fully autonomous navigation of truck, robot, drone
Following the object / person (semi-autonomous navigation)
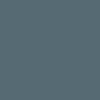
Do not waste your resources, let us show you how to save.
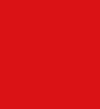