Wood Logistic System Slovwood Ružomberok, member of Mondi SCP
Location: Ružomberok
Function: integrated pulp & paper mill
Capacity: handling of 2 millions of cubic meters of wood p.a.
Employment: 1400
Slovwood serves transports and unloads tenths of trucks and wagons of timber in average on daily basis.
M2m products implemented: TLS
Background
It is a very challenging job to effectively plan and execute the logistics of timber from thousands of loading places.
Unbalanced delivery of the material („empty“ time slots versus rush during peak times) leads to traffic collapses on the roads near the unloading point.
Time demanding manual validation of contract fulfillment for individual suppliers
Ineffective information sharing between stakeholders ( suppliers, transport providers, operators, management)
These were main reasons why SLOVWOOD began to look for an information system to manage the whole supply chain.
Requirements
We have signed a contract to analyze and to implement the Wood Logistic System in June 2012 after a presentation of our Transport Logistic System that was already in use by another customer of ours.
Business requirements for WLS:
To manage delivery planning of the whole supply chain.
To ensure consistency and reliability of data for all business partners.
To have overview of all incoming vehicles + material and their arrival time slot for acceptance staff.
To allow organizing electronic tenders for truck deliveries.
On-line evaluation of contract fulfillment for individual suppliers.
To process and on-line evaluate the GPS data from trucks.
Communication with SAP in both directions.
Communication with an Attendance system.
Guaranteed system response.
Web client interface with user authentication.
Simple and user-friendly interface.
Transports organized into time slots and management of restrictions:
Wood suppliers may create transport request only if there is a capacity to process the material at the unloading point. Forwarders might reserve transport only within an free time slot based on the unloading capacity at the unloading point. Forwarder is capable to serve transport only from allowed loading places and his evaluation based on quality of service and price. The system also monitors and evaluates the actual transport performance based on GPS data from the GPS unit located in the forwarder's car.
Planning and organizing the whole supply chain:
- Material transport organized from the loading point directly in a forest or stock.
- Supplier and supply steering – material, quality and quantity.
- Weighting and delivery registration process done in system.
- Current process status information available on-line for all.
- System provides information on every subject in the whole supply chain, including a rating feature.
Using our development platform we have achieved the following:
- The first version of the WLS was released into the production five months after the contract was signed.
- Any data change within WLS triggers an automatic recalculation of their dependencies.
- Clear and swift reporting of information needed for decision making and future planning.
Seamless integration of the solution into the existing customer’s IT systems landscape (GPS data processing, integration with SAP, integration with scaling systems)
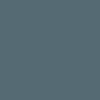
Results
- Optimized amount of effort required for planning and delivery control activities
- Considerable improvement of relationships with forwarders
- Optimized transport planning and transport load balancing
- No more unplanned deliveries
- Simple monitoring of transport efficiency and quality of delivery (in time, in expected quality)
After successful implementation of WLS we have made the following functionality updates:
- Integration with road scaling systems
- Integration with railway scaling systems
Future cooperation between M2M Solutions and Slovwood has already been planned. Further steps are:
- Unification of transport logistic approach for other wood commodities and customers
- Integration to additional wood trading systems
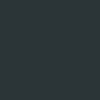
Do not waste your resources, let us show you how to save.
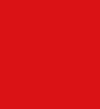